In the aftermath of Covid-19, many businesses are making a more concerted effort to address risks and exposures that were uncovered or made worse by the pandemic. The apparel manufacturing industry took a big hit financially, making it more essential than ever to protect the health and safety of workers as the industry recovers.
Now is the time for your clients to hit the reset button on employee health and safety; and thanks to Covid-19 protocols, many apparel manufacturers are already on the right path.
Keep going on controls started during the pandemic
Even before Covid-19 spread around the globe, minimizing airborne contaminants in the workplace—through controls like proper ventilation, use of personal protective equipment (PPE), and distance between workers—was a top-of-mind challenge for many apparel manufacturers.
“COVID-19 forced manufacturers to adapt quickly and to look for solutions higher in the hierarchy of controls,” said Foresight’s Head of Safety Success Drew Youpel. “So instead of going straight to PPE, they had to perform assessments, identify exposures, and use the more effective engineering and administrative controls to reduce their COVID-19 risk and comply with new guidelines,” he added.
OSHA released temporary Covid-19 guidelines during the pandemic, and many states are passing legislation to make some of these permanent. Even if your state isn’t, your client should consider the benefits of safety practices that could keep new and returning employees productive and protected from Covid-19 and other viruses that spread through the workplace.
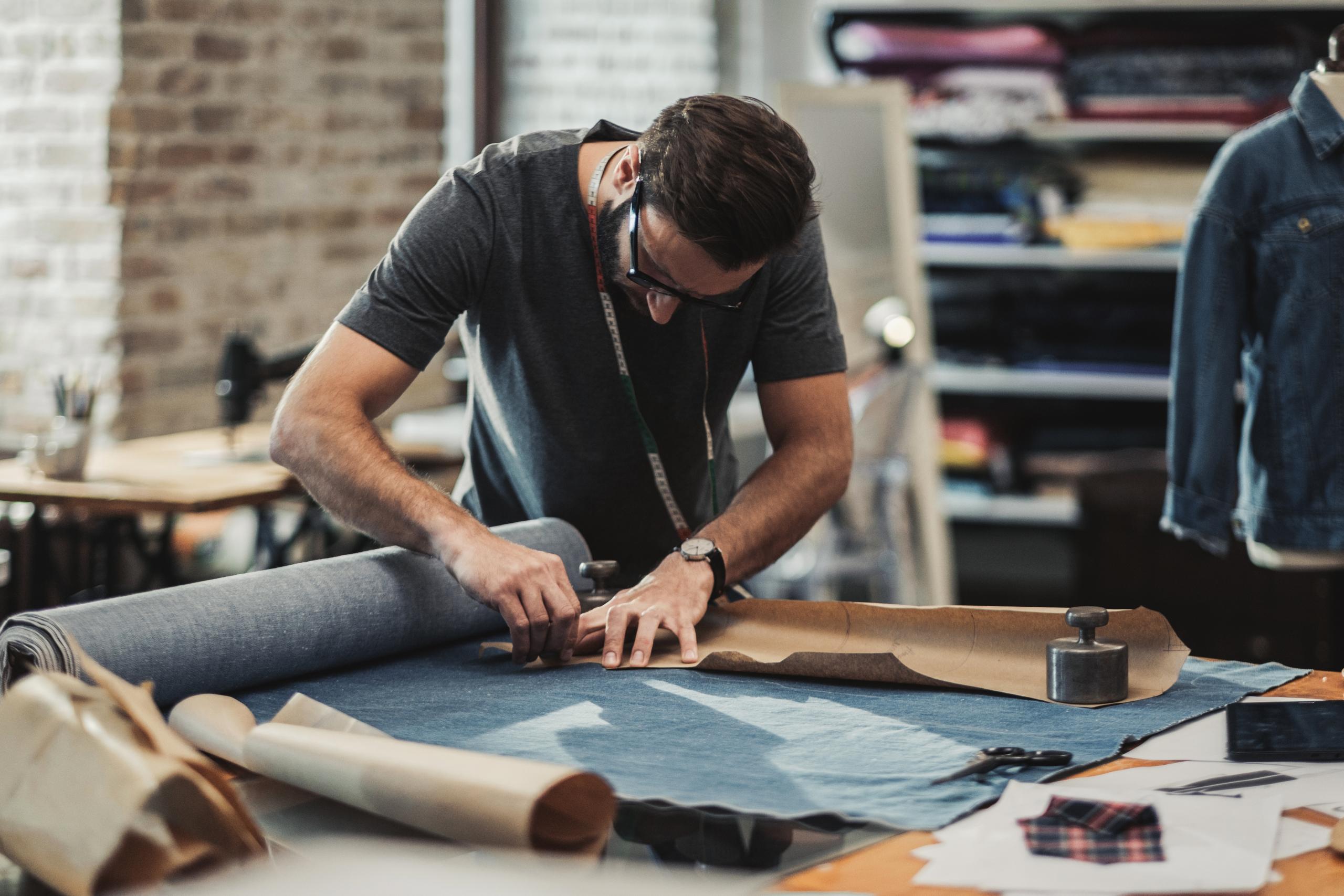
Where to focus for the most benefit
Your clients should take the time to create a cleaner, safer environment for their employees. Here are some focus areas that offer the most return on time, effort, and investment:
Improve ventilation: Simply by the nature of the job, garment workers can be exposed to a form of cotton dust that contains endotoxins, contaminants and bacteria that can cause serious respiratory problems. Proper ventilation can help reduce this type of dust in workspaces and address other indoor air quality issues. Upgrade dust-collection systems—using a cartridge dust collector more efficiently collects and expels dust. Update maintenance schedules and protocols for cleaning the systems, including filter servicing or replacement. A risk management technology system like Safesite can help simplify this process for your client. Keep temperature and humidity at proper levels since they affect air quality.
Provide effective PPE: Covid-19 took what was once a safety industry acronym and turned it into common vernacular. Apparel manufacturing companies stepped up to mass produce masks and other PPE for the public during the pandemic but shouldn’t forget about the urgent need for proper PPE in their own workplaces. Garment workers are exposed not only to dust, but also to chemicals used in fabric production when they handle finished material.
Provide respiratory protection, eye protection, and hearing protection where appropriate. The CDC recommends cloth face coverings for workers when physical distancing isn’t possible, but emphasizes that they are not substitutes for PPE in situations where respirators or facemasks are recommended or required for the worker, such as when working with certain chemicals.
Face shields offer additional protection against splashes and person-to-person droplet spread and can also work well for eye protection.
Redesign workstation physical distancing: Even when Covid-19 subsides, keeping workers physically distanced can help with the spread of other transmissible illnesses. Clients should pay attention to how workers are physically distanced not only at workstations but in other locations such as when clocking in and out and taking breaks. OSHA offers suggestions using the hierarchy of controls system:
Engineering controls examples include modifying the alignment of workstations so that workers do not face one another or using physical barriers such as strip curtains or plexiglass.
Administrative controls include staggering workers’ arrival and departure times and break times to avoid congregations of workers.
Step up cleaning and sanitizing: Good housekeeping and keeping the workplace clean and sanitized not only helps prevent the spread of illness, but prevents other risks such as fire and slips, trips, and falls. Some CDC recommended cleaning and sanitizing practices to continue include apparel manufacturers must continue frequent sanitation of work and common spaces, including wiping down tools and machines between shift changes. Wipe down frequently touched common surfaces such as door handles, push bars, and handrails that have qualified under EPA’s emerging viral pathogens program.
Expand employee training and communication: Encourage your clients to continue training and communicating with employees on the importance of preventing exposure to viruses. Make sure they’re aware of the control measures discussed here, and that all training, posters, and other safety communications are available in the preferred languages of your employees. The CDC recommends businesses educate employees on proper handwashing and use of hand sanitizer stations, cough and sneeze etiquette, and staying home when sick with a contagious illness.
But as Youpel points out, make sure the method of communication and training doesn’t become part of the problem. “Don’t train employees by bringing a large group into a room,” he reminds. “Use a mobile setting like we’ve made available on Safesite, and be sure to follow up on new controls with regular inspections.”
Stay a step ahead of possible workplace infections disease standards
Covid-19 sparked attention across the U.S. to infectious disease hazards in the workplace. Apparel manufacturing companies could soon be on the hook to comply with newly-imposed state or federal infectious disease standards. Working with a safety-focused workers compensation company like Foresight can help your client to stay in compliance with new regulations and, more importantly, to keep your workers safe and productive.