The size, nature, and economic importance of the construction industry make it a compelling study in workers compensation. Workers perform some of the most dangerous jobs there are, and an abundance of regulations exist to protect them. As a result, construction employers are predisposed to thinking about—and investing in—worker health and safety, since their safety record affects not only insurance costs and legal compliance, but also their ability to contract new work and to attract and retain employees.
The construction industry is changing in several ways that affect workers compensation risk management:
- The labor force is changing and becoming more diverse, partly because of a labor shortage that has lingered for over a decade and made worse by the Covid-19 pandemic.
- Regulations vary widely from state to state, and construction’s heavy representation in the Occupational Safety and Health Administration’s (OSHA) “Top 10” makes employers vulnerable to citations.
- Technology is quickly altering what the construction job site of the future will look like with drones, wearable sensors, and other mobile devices forcing the industry from paper-based to digital safety management programs.
- Loss trends in terms of both fatal and nonfatal injuries point to the need for employers to build behavior-based safety programs and to address the link between safety and employee health and wellbeing.
Since small to mid size construction firms make up the vast majority of the industry, insurance and risk management professionals need to step up and help employers navigate a high-pressure and rapidly changing industry.
In This Report: Construction and Contractor Trends
This report is based on industry trends and our own discussions with Foresight leadership and broker partners. Keeping an open dialogue with our brokers and customers on worker safety and workers compensation trends, issues, and challenges helps us band together to mitigate construction’s potentially deadly or life-altering risks. We created this guide as a succinct reference tool to help you stay on top of critical trends such as:
Construction Workforce Trends
Statistics Snapshot
- Severe construction labor shortage continues: Of the 10.4 million unfilled jobs in the U.S. by late 2021, 358,000 were in Construction, and experts expect the shortage to get worse, so the labor pool will likely be made up of older and less experienced workers along with a growing number of women and Hispanic workers.
- An aging workforce means more severe, costly injuries: About 40% of all construction industry workers are ages 45-64, and while more experienced workers are less likely to be injured by certain hazards, they’re more susceptible to others.
- Expanding the labor pool increases injury frequency: A study commissioned by the Center for Construction Research and Training found that 44.5% of injury claims were filed by workers with less than a year’s experience in construction, and 30.1% were from workers with less than six months on the job.
Why Construction Labor Shortages Lead To More Workers Compensation Losses
The Covid-19 pandemic intensified the construction industry’s labor woes, but the labor shortage was set in motion over a decade ago. Many skilled workers left when the Great Recession of 2008 hit, and since then Baby Boomers have been retiring faster than they can be replaced.
The labor shortage couldn’t come at a worse time—demand keeps going up in both the residential and commercial sectors, spurred on by a recovering economy, a nationwide housing shortage, and new jobs expected to be created as a result of the bipartisan infrastructure deal.
Why are workers so hard to find? According to an AGC survey, 72% of firms say available candidates are not qualified to work in the industry due to a lack of skills along with other factors such as failure to pass a drug test. But only about a third of respondents say they’re investing more in training and professional development.
Some firms are offering base pay increases, hiring bonuses and other incentives as a quick fix, but the long-term solution will require more involvement and investment in career-building programs starting at the high school level. Some construction firms are getting creative and partnering with government workforce development agencies or trying online strategies to inspire interest in construction as a profession. But these solutions will take time to have any impact.
Aging construction workers are prone to more severe injury and chronic health conditions
Because older and more experienced construction workers typically follow safety practices and precautions, their problem isn’t injury frequency, it’s severity. The physical demands of construction work have been proven to cause more chronic health conditions over time as compared to white-collar workers.
An extensive study of aging construction workers showed a higher risk for musculoskeletal diseases among construction workers, especially back problems and functional limitations such as extending arms. Workers also lose muscle mass and bone density as they age and are more susceptible to chronic inflammatory disorders such as arthritis. A study by the CPWR found that older construction workers are at a significantly higher risk of COPD than the general population.
This new generation of construction workers already has the mindset of engaging with technology to change behavior
Emilio FigueroaChief Insurance Officer, Foresight
These health conditions combined with other factors inherent in construction work—harsh weather, long hours, awkward postures, and heavy lifting—greatly increase the chances that older construction workers will suffer severe and costly injuries and medical problems.
Inexperienced workers prone to more frequent injuries
On the opposite end of the workforce spectrum are inexperienced workers whose injuries tend to be less severe, but more frequent. A study by the Construction Industry Research and Policy Center analyzed more than 9,000 workers compensation claims and found that 44.5% were filed by workers who had less than a year’s experience in the construction industry, and 30.1% were from workers with less than six months on the job. Key findings of the study show that:
- Small firms (less than five employees) had more inexperienced worker injuries than medium and large-sized firms.
- Severity is less an issue than frequency—injuries requiring hospitalization and major medical treatment were only slightly higher than the proportion of serious injuries among all workers.
- The most common causes of injuries among newer workers were lifting and strains, which resulted in injuries to the lower back, fingers, and shoulder.
“While it’s challenging for construction employers to fit inexperienced workers into their risk management practices, they should consider the advantages,” said Emilio Figueroa, Chief Insurance Officer for Foresight. “This new generation of construction workers already has the mindset of engaging with technology to change behavior, and when you use technology to encourage positive safety behaviors, you’ll see them forming good habits early on.”
How expanding the labor pool could impact workers comp issues
Ongoing labor shortages have the predictable effect of forcing employers to grow the labor pool. In the case of construction, such expansion has the positive outcome of creating well paying jobs for groups that might have been previously overlooked—such as women and minorities—but it also raises new safety issues.
About 10.9% of workers in the construction industry are women, but they make up only about one percent of workers on construction job sites. Calls for hiring more women into the industry are getting louder, and employers are considering how they can remove existing barriers and stereotypes that have kept women out of the industry. As they welcome more female workers, employers will need to consider the resulting health and safety concerns in the areas of ergonomics, personal protective equipment, hazards for pregnant women, and sanitary facilities.
With no real end in sight to the construction labor shortage, employers and their workers compensation insurance partners must be open to creative solutions and new tools when it comes to hiring, training, retaining, and keeping employees safe.
Hispanic/Latino immigrants are another at-risk population when it comes to construction injuries, particularly when they work for smaller firms and are 25 years and younger, according to a study by the American Society of Safety Engineers (ASSE) and the National Institute for Occupational Safety and Health (NIOSH). Fatalities among Hispanic construction workers are concerning, rising about 90% from 2011 to 2019 even though Hispanic/Latino workers only make up about 39% of construction payroll employment. Much of this discrepancy points to poor safety training and providing bilingual safety instruction.
With no real end in sight to the construction labor shortage, employers and their workers compensation insurance partners must be open to creative solutions and new tools when it comes to hiring, training, retaining, and keeping employees safe. The demographics of the construction workforce and how they conduct their work are changing rapidly, but fortunately so is the technology designed to protect them—from drones and exoskeletons to smart devices and handheld technologies.
Regulatory Trends Affecting Contractors
Hot Button Issues
- Vaccine mandates: Recently, vaccine mandates have gotten a ton of press coverage and to some degree, have been struck down by the Supreme Court, though it’s unclear how, or even if, they’ll come back. But whether or not these mandates exist in the future, employers need to pay attention to other infectious disease-related regulatory compliance brought to the forefront by Covid-19.
- Marijuana legislation: The trend toward state legalization/decriminalization of marijuana, whether medicinal or recreational, is possibly the biggest unknown for companies to watch. While there’s been no evidence of movement to legalize marijuana on the federal level, it’s clear the country is moving in this direction. If it does happen, eyes will be on OSHA regarding regulation and testing within the workplace. Legal marijuana produces difficulties not found with alcohol due to difficulty in testing intoxication level.
As new regulations are constantly being added along with the changes to current regulations, it’s imperative for brokers to have access to the most up-to-date information from the Department of Labor and National Council on Compensation Insurance.
Construction Heavily Represented in OSHA’s “Top Ten”
Avoiding OSHA citations is important not only to avoid the costs associated with them, but also to show external evaluators that the workplace is safe. The construction industry is especially vulnerable to these citations. In fact, of the 10 most-cited OSHA standards, three are attributed specifically to the construction industry: Fall Protection, Ladders, and Scaffolding. Additionally, all others in the top 10 could apply to construction depending on the project. That list includes:
- Fall Protection (5,424 violations)
- Hazard Communication (3,199 violations)
- Respiratory Protection (2,649 violations)
- Scaffolding (2,538 violations)
- Ladders (2,129 violations)
- Control of Hazardous Energy (2,065 violations)
- Powered Industrial Trucks (1,932 violations)
- Fall Protection Training (1,621 violations)
- Eye and Face Protection (1,369 violations)
- Machinery and Machine Guarding (1,313 violations)
One difficulty in predicting legislative and regulatory trends that could affect the construction industry lies in the fact that regulations are constantly changing and vary from state to state. But following some basic guidelines will reduce the chance of trouble:
- Watch head warnings: Regulatory compliance issues don’t appear out of nowhere; they are caused by workplace behavior. These warnings vary from industry to industry and company to company, so it’s important to develop an internal list and update it regularly.
- Develop a proper network: Businesses have less control over any subcontractors they use than with their own employees. It’s important to properly vet them before they start work: check all credentials, compliance history, insurance carried, and references to name a few.
- Track changing/differing regulations among states: Organizations should have processes and procedures in place to track these regulations variations for different projects and communicate applicable information to relevant project managers.
Navigating these regulatory compliance issues is vital to cost control and general workers compensation management.
Key Loss Drivers and Safety Practices
Statistics Snapshot
- A historically hazardous occupation: Construction worker fatalities make up about 20% of all worker fatalities in private industry. Every year 9.7 of every 100,000 construction workers suffer a fatal injury, which is the fourth highest in any industry.
- Falls still top the “Fatal Four”: Falls remain the leading cause of construction worker deaths at 36%, followed by struck by equipment, caught in between, and electrocutions—together making up the “Fatal Four.”
- Non-fatal injuries costly for employers: Each year, 1.7% of construction workers suffer an injury serious enough to miss work. Injury rates in construction average 71% higher than injury rates across all industries.
- Emerging risks include infectious disease, mental health and heat stress: The CDC estimated that nearly 60% of the construction force was at a higher risk for severe illness from Covid-19; construction worker suicide rates are among the highest of all industries; construction workers account for 36% of all occupational heat-related deaths.
The High-Cost Hazards of Construction Demand a Robust Safety Culture
Technological advancements in construction safety are being put into practice at an encouraging rate, but the nature of construction work keeps it firmly classified as one of the most dangerous occupations. Labor shortages, housing demand, and the construction industry’s standing as a critical engine of the U.S. economy all point to the need for diligence in keeping workers safe and employers productive and profitable.
Construction companies spend 3.6% of their total costs on workers compensation—more than double what other industries spend. Therefore, most construction employers are acutely aware of the impact their experience modifier has on their premium and are motivated to improve safety.
Leading causes of fatalities: the “Fatal Four”
For years OSHA has been tracking the “Fatal Four,” construction’s four leading causes of fatalities, as illustrated in this graph.
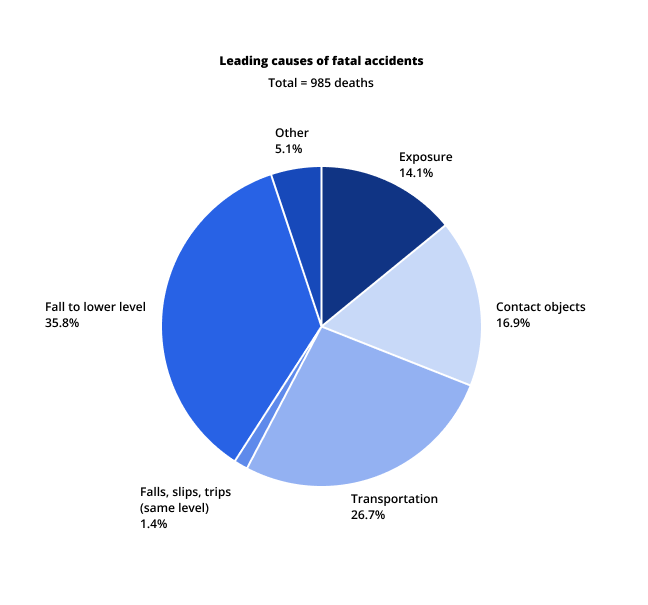
In addition to the “Fatal Four,” other fatality trends are cropping up that construction firms should note:
- The fatality rate for Hispanic workers in construction is higher than their white counterparts, but the gap is starting to diminish.
- Workers from firms with fewer than 20 employees make up a disproportionate share of fatal falls.
- Transportation incidents, where workers are struck by a vehicle that intrudes into a work zone or when construction vehicles and heavy equipment operate within a work zone, are a growing cause of fatal injuries.
Leading causes of injuries resulting in lost days away from work
The construction industry accounts for 8.5% of all injuries that result in lost days of work. In 2019 there were 112.3 injuries per 10,000 FTEs, which continued the steady decline that started in 2003, when the rate was 259.4 per 10,000 FTE. However, experts believe the number is likely much higher since many incidents go unreported—25% of construction workers surveyed by CPWR said they failed to report a work-related injury.
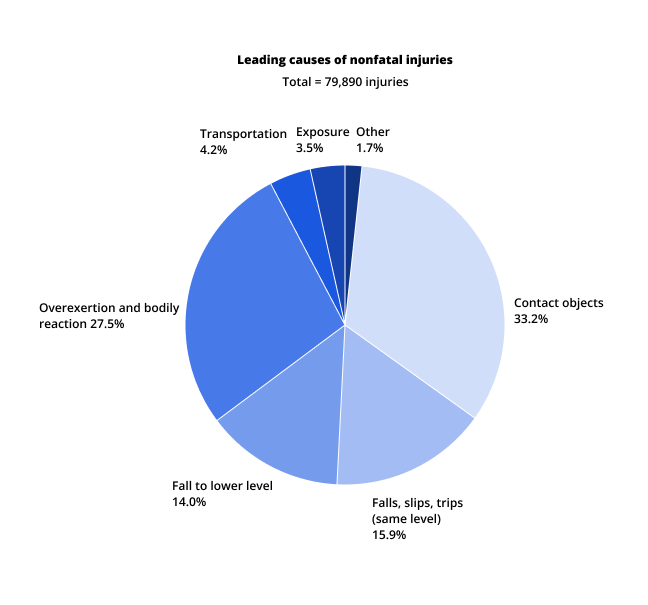
Emerging injury and health risks in construction
The causes of workers compensation injury claims across the construction industry change little from year to year, although some increase when certain disrupting factors come into play—such as more construction workers being struck by vehicles because more distracted drivers are on the roads.
The Covid-19 pandemic called attention to construction workers’ work-related illnesses and diseases, such as asthma and COPD, which increased their risk of severe disease. While studies have shown that these underlying conditions can stem from construction workers’ exposure to hazardous substances—such as dust, chemicals, and fumes—construction workers are also more likely to engage in certain health risk behaviors that can lead to work-related injuries, according to a recent NIOSH study.
All of this points to the need for health and safety risk management programs for construction workers that integrate safety and wellness. Some emerging health risks to watch in the construction industry include:
- Mental health: The construction industry has the highest suicide rate of any profession, and more than 80% of construction workers have experienced stress at work.
- Opioid abuse: A recent study connected the prevalence of musculoskeletal disorders among construction workers with higher prescription opioid use with their higher death rate from overdose compared to other industries.
- Heat stress: Construction workers account for the highest percentage (36%) of occupational heat-related deaths in the U.S.
Characteristics of an effective construction safety program
With the high cost of medical payments and missed work due to injuries and illnesses in the construction industry, employers—even small companies—are aware of the need for a robust safety and risk management program. Absences from injury and illness also cost business owners in terms of meeting project deadlines, hiring temporary workers, and numerous other indirect costs.
Construction safety is all about making workers aware of their surroundings and the hazards that exist, and then continuously nudging them to follow the right actions until the behavior is changed
Emilio Figueroa, Chief Insurance Officer, Foresight
With small and mid size companies dominating the insurance market—only 15% of construction firms have 1,000 employees or more—safety programs should be cost effective, easy to use, and engage job site workers.
OSHA’s “four pillars” are a good starting point for small-to-mid size construction companies to use to build a safety management program. They are (1) management commitment and worker involvement, (2) worksite analysis, (3) hazard prevention and control, and (4) training of workers, supervisors, and managers.
“Construction safety is all about making workers aware of their surroundings and the hazards that exist, and then continuously nudging them to follow the right actions until the behavior is changed,” Emilio Figueroa, chief insurance officer for Foresight explains. “When engaging technology is the source of that ‘nudge,’ and workers have a hand in continuously improving safety practices, Foresight data shows claims can be reduced by up to 31%.”
Key components of an effective construction safety management program include:
- Tracking and analyzing incidents, near misses and incident responses
- Performing root cause analysis, reporting, and trending
- Benchmarking to find areas of improvement
- Collecting and managing data for OSHA inspections
- Incorporating behavior-based safety training by identifying trends, fixing problems, and rewarding compliance
- Communicating safety issues in real time
An approach that works for construction employers of all types and sizes is to continually push behavior change through “high frequency/low touch” communications that keep employees aware of the hazards while they’re performing a particular task and prompting them to perform it safely.
Safety management technology, especially when it’s easily accessible to employees on their smartphones to encourage their participation, helps employers with these behavior-changing communications in addition to managing everything from incident reports to safety meetings. And when safety behavior improves, injuries are avoided, and lives saved.
Leading Safety Technology Trends for Contractors
Statistics Snapshot
- Growing adoption of tech: In a study from the U.S. Chamber of Commerce, 79% of construction contractors said improved jobsite safety is the top benefit that would encourage them to invest in advanced technology—ranking it higher than increased labor productivity and managing project schedules.
- Tech best for safety management: The technology contractors believe will positively impact worker health and safety are wearables (34%), virtual reality for training (32%), predictive analytics (28%), remotely controlled equipment (26%), and visual monitoring with AI (25%).
- Use of data: 34% of small and midsize companies report they collect safety data, but it goes unused; 13% of small and 17% of midsize use data to study trends and plan for improvement; less than two percent use true predictive analytics.
- Online safety training: Nearly two-thirds of all contractors use online health and safety training, but only about 54% of small firms use it.
Midsize Businesses the Key to Broad Safety Management Adoption
Construction companies are seeing new technologies introduced at breakneck speed. While most have been using high-tech tools in other aspects of their business, including digital design and project management, safety technology is still not as widely used, although usage increases every year. However, employers see the value of integrating technology into safety management—whether in the form of digital tools and devices, data gathering, or analytics.
As expected, large firms are using safety technology at a higher rate, but with the industry dominated by small-to-midsize companies, widespread adoption won’t take place until these companies have a cost-effective option that’s easy to integrate into their existing programs.
Job safety technology trends to watch
- Drones: Drones serve many useful purposes on construction sites and are becoming more commonplace. They give a bird’s eye view of potential hazards on the job site through remote pre-construction inspections and real-time site monitoring.
- Wearable sensors: A 2019 NIOSH study found that the active hazard in 73 incident reports examined in the study (29%) could have been prevented with a wearable device, such as a garment or other object with smartphone or “internet of things” (IoT) connectivity.
- Mobile devices and cloud-based mobile applications: Digitalizing safety processes from end-to-end through a tool such as Safesite helps companies improve compliance, training, and employee involvement while allowing for real-time monitoring of safety tasks and potential new hazards. Having the platform available on mobile devices allows employees to easily engage and respond faster to incidents and injuries.
- Data management and predictive analytics: A Dodge/CPWR study found that over 70% of small companies aren’t using data or don’t use what they gather, and they’re still too reliant on paper checklists and spreadsheets. Better digital data gathering allows for predictive analytics, which helps contractors perform root cause analysis and address the source to prevent reoccurrence.
2022 Outlook for Construction & Contractors
What will the construction site of the future look like? The labor pool will be younger and more diverse. Technology—whether in the form of drones, exoskeletons, wearable devices, or technology not yet imagined—will be heavily relied upon for safety management.
Technology exists today that could help construction employers of all sizes address the workforce, regulatory, and loss trends discussed in this guide:
- Inexperienced workers engaging with digital behavior-based safety tools and training available on handheld devices learn safe behaviors faster and more effectively, reducing accidents.
- Digitized OSHA recordkeeping, incident reporting, inspections, and audits help keep employers compliant and aware of changing regulations.
- Data gathered and analyzed from wearables, digitized incident reports, and employee observations quickly identifies safety problems so they can be addressed immediately.
There is a massive opportunity for incentivizing faster adoption of safety technology in construction companies. The sooner they start collecting quality data, the sooner the business and the industry as a whole can learn from it and make improvements that finally help construction companies turn the corner on injury prevention.